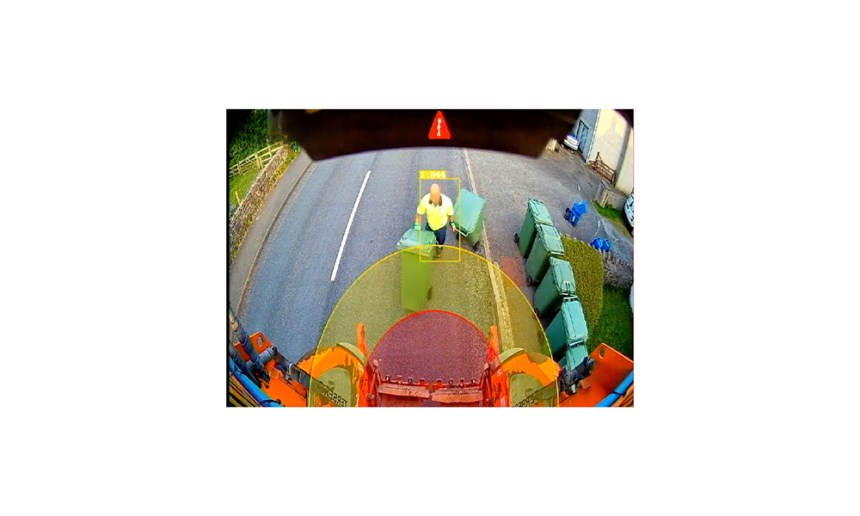
News in brief | CIWM Commercial Partner Updates 3 July
News updates written by CIWM’s commercial partners.
Contel launches next-generation AI camera systems to enhance fleet safety in the waste sector
Contel, a UK-based vehicle technology specialist, is helping waste and environmental service operators boost fleet safety and compliance with the rollout of its latest AI-powered camera systems.
Developed to address key risks such as blind spots and vulnerable road user collisions, Contel’s advanced AI cameras provide real-time analysis and alerts to reduce the likelihood of incidents, especially in busy urban and high-risk environments.
Optional in-cab cameras and intelligent software can monitor for signs of driver fatigue, distraction, mobile phone use, and external cameras can warn the driver to people or obstacles near the vehicle. When a potential risk is detected, the system gives the driver a visual and audible alert in real-time, helping them respond before a near miss turns into something more serious.
The AI camera solution can be installed alongside multi-camera DVR systems, and integrates fully with Contel Connected, the company’s telematics and fleet management platform. This means fleet managers can access live footage, receive instant alerts, and use the data to review driver behaviour or support ongoing training.
Andy Kelly, CEO and Co-Founder of Contel said: “Waste vehicles often operate in challenging environments, which often include narrow residential roads, early mornings, frequent stops, and reversing near pedestrians.
“Our AI systems are designed to help operators reduce avoidable incidents and give drivers extra support when they need it most.”
The technology also supports DVS and FORS compliance and is suitable for RCVs, sweepers, and other specialist vehicles. Contel offers UK-wide installation and support through its field engineering team.
To find out more, visit www.conteluk.com or contact the team at sales@conteluk.com.
CRJ Services | Revolutionary Maintenance: The HAAS TYRON Quick Change System Transforms Recycling Operations
Over the years, the recycling industry has occasionally accepted that high level equipment maintenance comes with significant downtime.
Replacing main machinery components often meant days of labour, specialised tools, and costly man hours. But that’s no longer the case with the Haas Shredder.
HAAS Recycling has introduced the groundbreaking QC – Quick Change System for its HAAS TYRON shredder, marking a major leap forward in maintenance efficiency and cost reduction.
The new Quick Change System centres on a revolutionary modular approach that allows complete shredding unit exchange in record time.
Unlike traditional systems requiring extensive dismantling and specialised expertise, the QC system separates the shredding unit entirely from the drive section, eliminating the need to access sensitive components like bearings or hydraulic lines.
Key technological advantages include:
Modular Design Excellence – Changeable components (counter combs, breaker bars, rotor shafts) allow one machine to handle diverse materials without compromise.
Hydraulic Quick Change Innovation – Simple hydraulic slide-out mechanism requires only basic screwing and lifting for component access.
Unprecedented Speed – Shaft changes in under 90 minutes, complete chamber replacement in 45 minutes.
Flexible Configuration Options – Different shredding tools maximise equipment utilisation across various recycling applications.
Robust Engineering – Asynchronous planetary gearbox with large bearings and maintenance-friendly coupling ensures reliability.
Cost-Efficient Service – Rotor shaft reconditioning via welding (dedicated device or in-machine) reduces costs and complexity.
Game-Changing Technology: Cuts Downtime from Days to Minutes
“This technology is a game changer for servicing both our hire fleet and third-party machines,” says Deon Swanepoel, Head of Engineering at CRJ. “What used to take over two days now takes under two hours—massively reducing downtime andboosting customer productivity. This is going to revolutionise our operations, particularly our swing machine programme.”
CRJ’s carbon emission reduction strategy seamlessly integrates Net Zero targets into our long-term vision, directly supporting SDG 13 (Climate Action) through innovative technology adoption.
The HAAS TYRON Quick Change (QC) System represents a transformative advancement in CRJ Services’ commitment to UN Sustainable Development Goals across the UK and Ireland, fundamentally enhancing waste management efficiency whilst delivering measurable environmental benefits.
As HAAS Recycling’s exclusive UK & Irish dealer, CRJ leverages this cutting-edge technology across our extensive hire fleet of TYRON shredders, maximising service efficiency for both hire equipment and third-party machines.
This comprehensive approach drives sustainable waste processing capabilities whilst substantially reducing carbon footprints, demonstrating our unwavering commitment to environmental stewardship and operational excellence.
Proven Performance, Enhanced Serviceability
The HAAS TYRON with Quick Change System maintains all the performance characteristics that have made it an industry standard, whilst adding unprecedented serviceability. The system’s design ensures that routine maintenance becomes a planned activity rather than an emergency disruption.
The separation of the shredding unit from the drive section represents sophisticated engineering that prioritises both performance and practicality. This approach protects sensitive components whilst enabling rapid access to wear items that require regular attention.
Looking Forward
The Quick Change System represents more than just improved maintenance procedures. It signals a fundamental shift towards equipment designed around operational realities rather than purely technical specifications. By acknowledging that maintenance is inevitable and designing systems to minimise its impact, HAAS Recycling demonstrates genuine understanding of customer needs.
For recycling operations seeking to maximise equipment utilisation whilst minimising operational disruption, the HAAS TYRON Quick Change System offers a compelling solution. The combination of proven shredding performance with revolutionary maintenance capabilities creates new possibilities for operational efficiency.
The difference is clear: where traditional systems create maintenance challenges, the Quick Change System creates maintenance efficiencies.
For more information about the HAAS TYRON Quick Change System and how it can transform your recycling operations, contact CRJ, the exclusive dealer for HAAS Recycling in the UK and Ireland. crjservices.co.uk
For more information on the HAAS Tyron Quick Change System click here.
Fleetclear | Fleetclear promises peace of mind with new DVR Health Report
Fleet technology provider Fleetclear is promising peace of mind to fleet operators with its latest offering – a DVR Health Report that provides fleetwide visibility to spot any issues with camera systems and fix problems before drivers know they exist.
Every fleet operator knows that frustrating experience when, at the crucial moment an incident occurs, a camera on the vehicle isn’t working and there’s no footage to verify what happened.
Ensuring equipment is fully operational is not only essential for safety reasons but is often a requirement for insurance policies. However, manually checking every camera and device on a large fleet is very time-consuming.
The Fleetclear DVR Health Report automates the process and detects any issues or intermittent faults across the entire fleet, pinpointing only those areas that require attention. It is in essence a regular, automatic check-up for the vehicle’s black box, ensuring that all cameras are online and working optimally, files are being saved correctly and there is adequate storage.
Chris Waller, Chief Technical Officer, Fleetclear said: “The health report turns the DVR system into a proactive safety tool and saves a huge amount of time by automating the process of checking equipment.
“As part of the process a snapshot from each camera is taken to check the alignment and flag up any obscured views. The system can also target intermittent faults or crashes that may occur at random times with certain cameras.”
Each time the DVR powers up, a comprehensive health check is performed, snapshots of every camera are saved, along with any historical events or issues, and flagged for analysis on the Fleetclear Connect web app.
There is a choice between either a self-service option or a fully automated preference with automatic failure notifications, manual camera alignment checks, engineer scheduling and weekly email report.
Nuclear Waste Services | Designing for long-term safety of the most hazardous radioactive waste
Professor Lucy Bailey, Chief of Disposal Safety at Nuclear Waste Services on why a GDF is the ‘safest solution’.
The purpose of a Geological Disposal Facility (GDF) is to make the most hazardous radioactive waste permanently safe, sooner, removing the burden on future generations. Without it, for thousands of years, our descendants would have to carry the risk and pay for the costly enduring surface storage.
Geological disposal facilities use engineered barriers to work alongside the natural barrier of deep, stable rock hundreds of metres below the surface. This multi-barrier approach isolates and contains waste to prevent radiation from ever reaching the surface environment at levels that could do harm.
A GDF will be a passively safe facility, meaning that the facility will remain safe, for hundreds of thousands of years, without needing any human interaction, without the need for any inspections, any maintenance, or any repairs.
Multiple barrier approach
The geological barrier will provide the isolation, meaning it will keep the radioactivity away from people and the environment for very long timescales. Geological timeframes span millions of years and in the right geology, deep underground, we can be confident of a home for our wastes that will be stable for the long time needed.
The waste itself is processed, conditioned and packaged in solid form and put in suitable containers. These containers are placed underground in the tunnels and vaults within the GDF. The containers are surrounded with a buffer or backfill material (such as clay or cement) to protect the containers.
The tunnels and vaults, and all GDF accessways are then backfilled and sealed to secure the GDF. We refer to these as our “engineered barriers” and they will be specifically designed for both the wastes and the geological environment.
This provides us with a multiple barrier system to isolate and contain the waste. We are not relying on any single barrier and even if something unexpected affects one barrier, the others will still contain the radioactivity long enough for it to decay to levels that won’t cause harm.
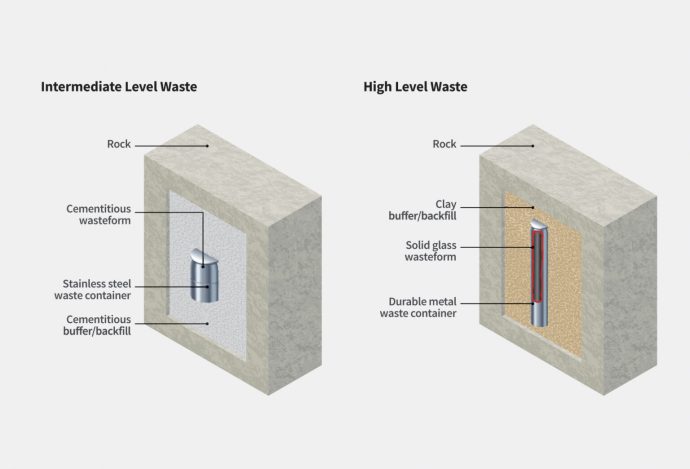
CASE STUDY: Cigar Lake – Canada
Cigar Lake is a naturally occurring uranium deposit in Canada. Cigar Lake is approximately 1.3 billion years old, the uranium ore lies about 450 metres below the surface and is enveloped within a clay rock formation.
Clay and rock have contained the uranium such that there are no significant levels of radioactivity detected at the surface above the Cigar Lake uranium ore body. Natural systems like this provide scientists with a long-term evidence base for the stability and safety of geological disposal.
Natural systems, like Cigar Lake, cannot fully replicate all the features of a Geological Disposal Facility, but they do provide insight and information on the long-term processes that isolate and contain radioactivity. These case studies can provide important evidence for the long-term safety concepts for geological disposal – proving that the right geology can provide the solution to disposing of radioactive waste.
Over timescales that long, there are many uncertainties. Working with Nuclear Waste Services (NWS) colleagues and international experts, it’s my job to identify relevant uncertainties, assess how they could affect the safety of a GDF, and work out how to address them in our design.
This work is how we build our Safety Case. A GDF can only go ahead if we make a strong Safety Case; it’s how our independent regulators (including the ONR and the EA) will determine whether our design is safe.
Implications for the very long-term future
To understand what could potentially affect safety and when, we can look at the future evolution of a GDF as a series of different phases with different conditions.
In the years immediately after the GDF is closed and sealed, the high heat generating waste in the vaults will be at its hottest. There will be some short-lived changes in this period as the facility and its environment settle. So, we need to take this into account with the design of our containers and the GDF.
After the short-lived changes of those early years, we expect about a thousand years of stable conditions. And in the very distant future, over hundreds of thousands of years, glaciation or tectonic activity could significantly change the landscape. Our multi-barrier approach takes all of these scenarios and changes into account, ensuring long-term safety.
Using data and case studies to evidence safety
Our work to support the development of a safety case for the GDF involves assessing all available data and commissioning the investigations needed to gain understanding of all processes relevant to the safety of a GDF. A synthesis of all this information will be required to secure the necessary regulatory permissions to build a GDF and will be key in the development of a GDF design and safety case.
We also have to identify any future scenarios that could impact the safety and security of a GDF. We look to cover everything from worst credible case scenarios to what-if scenarios.
In any worst credible case scenario, we take an event or uncertainty and ask, what is the worst possible moment that this could occur or the worst way in which something could happen? For example, what if people inadvertently drilled into the GDF as soon as the site was no longer being managed, when the level of radioactivity inside was still high? Preventing this scenario is one reason we’re planning to build the GDF so deep underground.
And a what-if scenario is something that we really don’t expect to happen, but that we consider anyway, as a way to challenge the robustness of our design. For example, we don’t think any of our waste canisters would ever totally fail – but our Safety Case shows that if one did, and radioactive material escaped from its container, the other engineered barriers and the surrounding geology would still prevent that material from endangering anyone on the surface, maintaining the right level of safety.
In 1999, the Nuclear Energy Agency created an international database of all the Features, Events and Processes (FEPs) that had been identified and considered by radioactive waste disposal scientists across the world. Since then, the database has been updated many times, but no significant new FEPs have been identified – so we’re confident we’re considering all the right things.
What’s the right level of safety?
For a GDF, our independent regulators define safety in terms of the dose of radioactivity someone would experience on the surface, measured in milliSieverts.
Every day, every one of us in the UK is exposed to a natural dose of about 2.7 milliSieverts, just from the natural background levels of radiation in our environment. The regulators will only judge a GDF to be safe if our Safety Case can show them that the additional dose on the surface would be 0.02 milliSieverts a year or less. That’s less than one percent of the natural background radiation level.
At the end of the day, if we can’t show that a GDF will be this safe or safer, it won’t happen. This means being confident in the safety ourselves, convincing our peer reviewers, including international peers, our community and other external stakeholders and ultimately satisfying the rigorous scrutiny of our regulators that a GDF is, and will always remain, safe.
Textile Recycling International | Textile Recycling International’s Group Recycling and ESG Director, Peter Page, headlines the inaugural Landfills2Landmarks Summit in Accra, Ghana
TRI was the headline sponsor for the first event held in Ghana to bring together those tackling the environmental damage caused by textile waste.
The Landfills2Landmarks summit held in Accra, Ghana on the 23rd and 24th May 2025 was the first event of its kind. It brought together government, secondhand retailers and their representatives, members of the Ghanaian fashion industry and those leading the textile recycling industry in the UK, many of whom are key suppliers to Ghana’s thriving secondhand clothing industry.
TRI played a key role in the creation of the summit, not only investing as a sponsor, but as the largest supplier of sorted and graded secondhand clothing from the UK to Ghana, highlighting the status and position of the UK Textile Recycling Industry.
The event consisted of engaging panel discussions and a vibrant Ghanaian cultural showcase. The overall focus was to reinforce the urgent call for accountability, innovation, and sustainable transformation in Africa’s fashion and textile sectors.
Peter Page, Group Recycling & ESG Director at TRI was keen to support the summit when he heard about the plans from the founders of Landfills2Landmarks, Samuel Ofori-Gyapoh and Henry Treku .
He said: “We thought this was long overdue and a very welcome opportunity for the Ghanaian textile recycling industry stakeholders to share what they’re doing to address the issues and leverage the opportunities for textile recycling in Ghana.”
In his headline speech, Peter called for the Extended Producer Responsibility (EPR) generated funds expected to be applied to new clothing in the UK, to be directed to Ghana where secondhand clothing that originated in the UK meets end of life.
He said: “EPR is not just a policy tool, it is a cornerstone of the transformation we must learn together. Imagine a world where every garment is reclaimed.”
The Honourable Issifu Seidu, Minister of State, Climate Change and Sustainability, in his speech at the summit said, “With your support, we are capable of turning the waste into wealth…let us build this future now.”
TRI’s work with the Landfills2Landmarks team in Ghana continues with potential projects that support the building of a textile recycling infrastructure that can process Ghana’s waste clothing.
Peter added: “The Landfills2Landmarks experience in Accra was one of energy, focus and innovation. For TRI, it starts with making sure we send fully sorted, secondhand clothing that the retailers in Ghana can sell on to their citizens. It ends with supporting recycling infrastructure to divert these clothes at end of life from waste to resource.”
WasteRecruit | Connecting green skills and culture
An opportunity for the resource sector to influence the future of business.
Employees and customers alike both rate sustainability as important in choosing which companies to work for and buy from. However, there’s an illusion that commitments automatically translate into targets, which, in turn set the course for business. Statistics tell a different story.
According to Accenture, 93% of companies will fail to meet their sustainability or net-zero targets by 2030. Evidence that promises are not enough and that green skills gaps, remain wide. Without the knowledge on how to scale sustainability efforts, roadblocks occur and promises are quickly diluted, delayed, or simply forgotten altogether. It seems that while companies recognise the importance of sustainability, presenting strong annual financial reports matter more.
Herein is the root of the problem. It’s not the desire for profit, or even the pursuit of it. It’s the belief that profit matters more, and that any costs to achieving it are acceptable. If we hope to reverse the trend of companies not achieving sustainability targets, this is the culture that needs to change. Can developing green skills achieve this?
Belief in the economic case for sustainability
The resource sector is filled with people who have both the skills and understanding of the challenges associated with changing business as usual. They’ve had to deal with the growing waste volumes and try to find solutions for contamination. They’ve been frustrated by policy and the lack of understanding associated with sustainability efforts.
But they also recognise the opportunity for improved profitability if the culture of business changes, including practices that look beyond optimising waste management and recycling. Theres consideration for material inputs, finding productivity efficiencies, and developing connected systems reintegrating outputs from one process into inputs from another. All while believing that the effort is worthwhile, will be profitable and deliver the desired return on investment.
There’s mounting evidence that sustainability can indeed be profitable.
- In 2024 the green economy grew by 10% – 3 times faster than any other sector.
- This effectively mutes the debate that there needs to be a trade off between sustainability and profitability.
- Reuse can deliver massive cost savings to businesses with the potential to increase profitability. Highlights from a recent report on reuse in the UK:
- Aiming for a target of 30% reuse in packaging could save between £300m and £500m worth of system costs per annum.
- This would save producers more than £130m in associated EPR costs.
The human challenge – cultural change
Despite the evidence, the challenge remains in getting humans to change their habits as well as their beliefs because this is where impact happens. Understanding potential benefits associated with sustainability requires follow up. Intention is only the start, it takes skill, coordination and cooperation to successfully implement strategies.
Most importantly, people need to understand why there’s a need to change the way of working that’s been in place for decades. The ability to influence, gain buy-in, engage with people and take on board their perspectives – these are not commonly viewed as green skills. Yet without these skills, efforts to change behaviour are hard to achieve. Especially when that change needs to extend to suppliers, vendors, distributors or contractors.
Where does this place green skills?
There’s no question that the value of green skills in business is growing. As companies broaden their understanding of what sustainability and circular economy principles involve, it comes with a stark realisation that it’s not business as usual with a tick box on a compliance form. The problem is filling the gap. Connecting the dots and identifying what changes need to be made.
The waste and resource management industry has exceptional talent. Expanding and embedding that talent into all industry sectors will bring knowledge and practical experience where it’s most needed.
Thoughtful placement of people, matching their green skills with what the industry needs has the potential for significant impact.
Those with green skills know what a better way of doing business looks like and have the knowledge to drive change. Imagine the opportunity for business to harness that as a competitive advantage.
Vision Techniques | Vision Techniques join waste industry professionals raising vital funds for Bowel Cancer UK
Commercial Vehicle Safety and Security specialists, Vision Techniques, took part in the Miles4Miles Charity Bike Ride in memory of Jon Miles last month and raised a total of £570.
On June 13, Sales Director Dave Prince joined a group of waste industry professionals and cycled approximately 30 miles from Tunbridge Wells to Eastbourne raising money for Bowel Cancer UK in memory of Jon Miles – a man who dedicated over 30 years to the waste industry.
Managing Director Dave Smith also took part in the charity ride driving the support vehicle to make sure everyone was well.
As a collective group more than £11,000 was raised for the charity – and the team of riders are thrilled.
Dave Prince said: “It was a really nice route after the lumpy start with the hills. The second half of the route down the Cuckoo Trail into Eastbourne was a lot better.
“We celebrated at the end with a beer or two and an Italian. Total raised so far is just over £11k collectively. My bottom took some time to recover and my legs were feeling it for a few days after!
“I am really glad myself and Dave took part, fundraising activities like this go a long way to support charities who need donations.”
What an incredible achievement for all who took part.
Support in the form of a donation can still be given, if you would like to donate, you can do so here.
Vision Techniques are the innovative driving force in vehicle safety and security systems, protecting not only vehicles but also the lives of employees, the public and the environments they operate in.
Loved by some of the largest fleets in the UK, Vision Techniques’ products are influencing and changing safety and security standards across industries daily.
Wood Recyclers’ Association | UK waste wood market remained buoyant in 2024 with over 96% of material processed
The UK’s waste wood market remained buoyant in 2024, with strong demand for material, according to the latest annual statistics published today by the Wood Recyclers’ Association (WRA).
Of the 4.5 million tonnes of waste wood arising in the UK last year, the vast majority (4.33 million tonnes) was sent for reuse, recycling or recovery – equivalent to over 96%.
This achievement was similar to the 97% processed in 2023 – and may in reality have represented a slightly higher percentage given that limited activity in the construction sector may have slightly reduced waste wood arisings compared to previous years, according to the WRA.
The 2024 figures were compiled by the WRA using its annual survey of members who handle approximately 90% of the waste wood market by volume. These figures are extrapolated, alongside latest industry data, to produce figures for the whole of the UK.
Other key takeaways include:
- Large-scale biomass continued to be the largest end user of waste wood during the year, accounting for 2.8 million tonnes (65%) of material (no increase from 2023). This demonstrates the sector’s important role in delivering secure, renewable baseload power.
- The panel board industry remained the second largest user of waste wood, using over 920,000 tonnes of waste wood (21% of processed material). This represented a small (4.5%) decrease compared to 2023, due to the depressed housing market and the closure of the West Fraser South Molton manufacturing plant.
- The amount of waste wood used for animal bedding, equine surfacing, other recycling and reuse decreased 11% year-on-year to 310,000 tonnes. This fall was linked to reduced demand for poultry bedding due to avian flu, alongside reduced construction activity impacting reuse.
- Pallet refurbishment and reuse of wooden items through local authority reuse hubs increased during the year – something which is excluded from the figures but which the WRA hopes to report on in future.
- Exports/imports netted off rose 2.8% year-on-year to approximately 211,000 tonnes, representing 5% of the market. This was due to high demand for biomass feedstock in Europe.
- Usage in small scale biomass remained static at 90,000 tonnes, representing 2% of the market.
Julia Turner, Executive Director of the WRA, said: “These figures show the UK waste wood market remains balanced and in great shape with well-developed and environmentally compliant markets for all domestic material.
“We are very proud to say that nearly all waste wood is being utilised, with only a very tiny fraction being sent to informal markets, such as being burnt on bonfire night, or being sent to landfill. In this way our sector plays an important role in supporting the circular economy, net zero and energy security in the UK.”
“For our industry to maintain this performance in 2025, it is important that sites are able to store material over the summer months for when it is most needed. This is why we are calling for the Environment Agency to ensure that its recently-announced Regulatory Position Statement 352 is not too restrictive, and allows waste wood to be stored safely and compliantly for long enough that it can be used through the coming winter.”
To accompany these statistics, the WRA today unveiled the sector’s latest carbon emissions savings figures.
These show that the UK panel board sector sequestered 1.09 million tonnes of carbon in 2024 through its use of recycled wood in chipboard.
And, waste wood biomass continued to save 701,000 tonnes of carbon emissions in 2024 when compared to the likely displaced generation, with the potential to save 3.6 million tonnes with carbon capture and storage (CCS) – Figures calculated using a model independently verified by Kiwa.
Julia said: “Our latest carbon savings figures highlight how our sector is helping to drive down emissions by both locking away carbon in panel board products and displacing fossil fuels. Our contribution is even greater if you take in account the carbon savings achieved through other recycling and reuse, which we hope to report on in future.”
EPIC MEDIA | Waste Industry Rides in Memory of Jon Miles, Raising Over £11,000 for Bowel Cancer UK
A group of dedicated professionals from across the UK waste and recycling sector recently took on a two-wheeled challenge to honour the memory of their much-loved friend and colleague, Jon Miles, raising over £11,000 (and counting) for Bowel Cancer UK in the process.
The cycle ride, which covered a scenic yet testing route from Tunbridge Wells to Eastbourne, brought together people from all corners of the industry who had been touched by Jon’s warmth, leadership, and commitment throughout his distinguished 30-year career.
The group was proudly supported by a number of key suppliers and stakeholders, including EPIC Media Group. Among the riders was EPIC Media’s Founder and now Business Advisor, Kevin Murton, who paid tribute to Jon’s legacy:
“Jon was a husband, a son, a brother, a father, an uncle and a grandfather. He loved his family very much and was incredibly proud of them all, including Benny the dog. To others, he was a friend, a colleague, a boss, a confidant and a mentor.
He touched so many lives, and in fundraising for Bowel Cancer UK, we celebrate an extraordinary man who gave so much to others, both in and out of work.”
The ride was not only a personal tribute to Jon but also an important awareness-raising event for bowel cancer, which remains one of the UK’s most common cancers. The fundraising effort aims to support Bowel Cancer UK’s work in providing essential research, education, and support for those affected.
The initiative has already surpassed its initial fundraising goal, with over £11,000 raised, and donations are still coming in. The campaign has been a poignant reminder of the strong sense of community within the waste and recycling industry and how it continues to come together in times of loss and purpose.
To support the cause or find out more, donations can still be made via the JustGiving page.
Alfred H Knight | Alfred H Knight and South Ayrshire Waste Analysis Case Study
With Simpler Recycling deadlines looming and other waste-like policies, Alfred H Knight reflect on their partnership with South Ayrshire Council and the waste composition analysis carried out.
The council required an analysis of their waste streams to address local information needs and help Zero Waste Scotland produce national estimates of household waste composition.
The local authority operates regular collection services of residual waste, food waste, dry mixed recyclables and garden waste from 59,000 households in the area. Residual waste is collected on a three-weekly basis, with dry mixed recycling such as plastic, metal and cartons collected separately from paper and card every four weeks. Food waste is collected weekly, with glass collected every six weeks.
The challenge
South Ayrshire Council received funding from Zero Waste Scotland to complete a waste composition analysis (WCA) of the household waste streams collected by the Council. They needed to assess the varying types of waste being deposited in their bins to determine the success of their current waste collection schemes and for future operational modelling.
Without evidence of the type of waste being disposed of via the residual waste and metals, plastics and carton collections, South Ayrshire Council could not propose the changes necessary to improve collections and operations.
Expert composition analysis
Alfred H Knight was chosen by South Ayrshire Council through the Zero Waste Scotland framework to carry out an analysis of residual waste, metals, plastics and carton collections from 250 households across 5 demographic groups.
As an industry-leading inspection and testing company, we worked in partnership with South Ayrshire Council to deliver clear and concise reporting on the composition of their domestic waste streams.
Paul Dougall, Coordinator of Neighbourhood Services at South Ayrshire, said: “The service provided by AHK enabled us to see that there was a significant quantity of food waste being disposed of in residual waste, despite a weekly food waste collection being in place.
“This information will shape and inform future collections and communication campaigns throughout the local area conducted by the Waste Team at South Ayrshire Council.”
Plan B | Plan B delivers unique materials management model at Essex HWRCs
Plan B Management Solutions Limited (Plan B) has managed the materials marketing for Essex County Council’s (ECC) in-house HWRC services since April 2022 in an industry first contracting arrangement.
Following a competitive procurement procedure, Plan B manages all aspects of onward material sale across the 21 HWRCs, working closely with ECC.
The contract is for an initial three years including the ability to extend, with Plan B managing approximately 70,000 tonnes of materials per year across 30 material types. The hybrid contracting arrangement provides ECC with a number of benefits including increased visibility and choice of onward destinations, ability to test and trial new material streams and a gainshare mechanism to incentivise innovation.
Plan B employs a local team on the ground in Essex who manage offtakers’ performance and audit sites to support material quality and back office support who collate all data culminating in a monthly report, including compliance and due diligence data. The on the ground staff are based in a Plan B office close to the ECC logistics team, and administration is carried out at Plan B central administration office in Great Yarmouth.
Through the contracting arrangement, Plan B provides ECC with improved visibility and a choice of onward destinations for their collected materials. Regular offtaker reviews through benchmarking exercises are undertaken to allow ECC to fully consider recommendations based both on financial and environmental considerations. Plan B shares market information and benchmarking analysis with ECC to assist with budget setting and service forecasting.
Other features of the contracting arrangement include no constraints of exclusivity or guaranteed minimum tonnages to allow the flexibility to test and trial new material streams and the ability to promptly switch offtakers. The contract also includes an aspect designed to incentivise innovation via the separation and management of new materials. This is managed using a gainshare mechanism within the contract.
Notable contract achievements include supplying over £8m of work to local businesses within county, capturing 5,251 tonnes of material for reuse and delivering over 38,000 items to local food banks in Essex as part of our social value commitments. ECC has also benefited from the exposure to improved market information to help develop and enhance its in-house team capability and understanding of materials marketing.
“Since April 2022, we have partnered with ECC to develop this unique approach to the management and onward sale of materials which has been recognised by WRAP in the recent 2025 Household Waste Recycling (HWRC) Guide” says Craig Cutajar, Materials Director at Plan B. “It has been really pleasing to demonstrate that we can deliver a successful contract aligned with Plan B’s mission and values and deliver something a little different in our industry.”
Craig adds: “We are actively exploring opportunities to work with other local authorities who would benefit from a similar contracting arrangement and are interested in a genuine partnership working approach.”
Greyparrot | Greyparrot launches Deepnest to help brands track packaging’s life beyond the bin
Greyparrot has launched Deepnest, the world’s first AI-powered waste intelligence platform for brands and packaging producers.
The company says that Deepnest gives packaging producers and brand owners access to real-world waste data, bridging a long-standing information gap between those designing packaging and those recovering it.
Powered by live data from Greyparrot’s AI waste analytics system, the platform gives brand owners unprecedented insight into how their packaging performs once it enters the waste system — enabling them to support more effective, profitable recycling.
Deepnest is already being used by the likes of Unilever, Asahi and Amcor to design products that are designed with the waste system in mind.
Tackling recovery challenges with real-world data
Despite advances in packaging design, a large amount of technically-recyclable materials still fail to make it through the sorting process. According to Greyparrot’s COO Gaspard Duthilleul, that’s because brand owners haven’t had visibility into how these materials perform in real-world recovery systems:
“Too often, packaging that’s theoretically recyclable never makes it through the system as intended. Either it can’t be correctly identified by the sorting machines, or it’s made from materials with no viable end market,” said Duthilleul. ****“That’s why we built Deepnest — not just for brands, but to take a systemic approach that supports the entire value chain. Waste managers need packaging to be designed for recovery, and brands need to understand what works and what doesn’t in real-world conditions, and at scale. Deepnest helps close that loop.”
In 2024 alone, Greyparrot’s global Analyzer systems detected more than 40 billion waste objects. The company says that level of real-time granularity sets Deepnest apart from the static recyclability tests and lab-based assessments that brands currently rely on.
Actionable insights for both brands and recyclers
With data from global recovery facilities anonymised and aggregated at a national or global level, brands and packaging producers can use Deepnest to:
- Benchmark recovery performance against industry peers
- Test and compare packaging formats within sub-brands before scaling
- Identify design features that hinder recovery in priority markets
- Quantify the impact of sustainability initiatives and redesign efforts
Producers’ newfound ability to optimise their packaging’s end-of-life journey is a major step forward for the waste and recycling sector:
According to Greyparrot, Deepnest enables recovery-friendly design improvements that boost material recovery, cut contamination, and enhance sorting efficiency and profitability — ultimately benefiting the entire packaging value chain.
Closing the loop with ecosystem-wide collaboration
In response to the Deepnest launch, waste management organisations like Biffa have spoken about the critical importance of closing the information gap between brands and the waste sector. Amy Hooper, Biffa’s Head of Innovation, sees this as an opportunity to foster closer collaboration across the value chain:
“We’re always looking for ways to strengthen the connection between what happens in our facilities and the decisions being made upstream,” said Hooper. “Collaborating with Greyparrot on the introduction of Deepnest allows our sector to help surface new layers of insight on material recovery for the broader value chain. Initiatives like this have the potential to help close the gap between ambition and action on circularity.”
Global brands like Unilever, Asahi and Amcor are early adopters of the Deepnest system, using it to assess packaging peformance and prepare for upcoming regulations like EPR and virgin plastic taxes:
“The packaging industry relies on lab-scale testing and software models to predict recyclability of packaging solutions,” said Mark Roberts, Circular Economy Director at Amcor. “Real-life data is missing, given the huge resources it would take to gather it at scale in recovery facilities. Deepnest is unlocking recyclability data that the packaging data chain has been missing.”
“Our goal is to reduce our virgin plastic use and make our plastic packaging reusable, recyclable or compostable,” added Dr Liz Smith, Global R&D Head of Deoderants at Unilever. “insights like these could critically help to inform future packaging design, enable recyclability in practice and at scale, and increase the supply of high-quality recycled materials.”
Sandra Gibbs, Chief Supply Chain Officer at Asahi Beverages, said Deepnest aligns with their broader investment in circularity:
“We co-operate Australia’s largest PET recycling facility, and we’ve been looking for real-time data to help maximise its impact … We installed Greyparrot Analyzers to unlock operational data to improve recycling quality and output. Deepnest can transform that data into insights that guide smarter packaging design from the outset. We’re exploring how this technology can help us embed a data-driven approach across the entire packaging lifecycle, moving us closer to 100% circular packaging.”
Optimo | Events and awards season for Optimo
It’s been a busy month of recognition and collaboration with key voices from Optimo and EMR Metal Recycling taking to the stage at ReGeneration Earth to share insight on the future of sustainable waste management.
Danielle Heward, Founder of Optimo | Certified B Corp, joined Habiba El-Gharably (NuGreen Ltd | KTP Associate with Leeds Beckett University) and Alastair Little (EMR) on the panel “From Waste to Wealth: Regional and National Solutions for Sustainable Waste Management in the UK”, chaired by Jonathan Straight FRSA at Regeneration Earth, part of the Yorkshire Sustainability Festival.
The wide-ranging discussion explored funding, policy, behaviour change, and the importance of scaling regional innovation into national circular solutions.
Alastair Little highlighted how Corporate Social Value and investment in recycled material end markets are helping reduce friction across the circular economy. “The level of innovation we’ve deployed across our network positions us well for future market demands and upcoming legislative shifts,” he said.
Danielle talked about the mindset shift needed to move more to a circular economy. “Tech, innovation and the passion of organisations in waste management to make the world a better place are all contributing factors to the behaviour change we need”.
The event formed part of a wider series of activities for Optimo this month. Founder Danielle Heward was also named ‘Impact Driver of the Year’ at the Climb UK Awards 2025, which recognise social entrepreneurs who are building mission-led businesses with measurable impact.
Reflecting on the momentum, Danielle commented, “Collaboration and transformation are more important than ever before. It’s been fantastic to share insights and support organisations driving real change on the ground.”
With panel appearances, industry showcases, and award wins all in a matter of weeks, this month has underlined the fast pace we are moving towards a better future — and the central role CIWM partners are playing in accelerating the transition.
The post News in brief | CIWM Commercial Partner Updates 3 July appeared first on Circular Online.

